
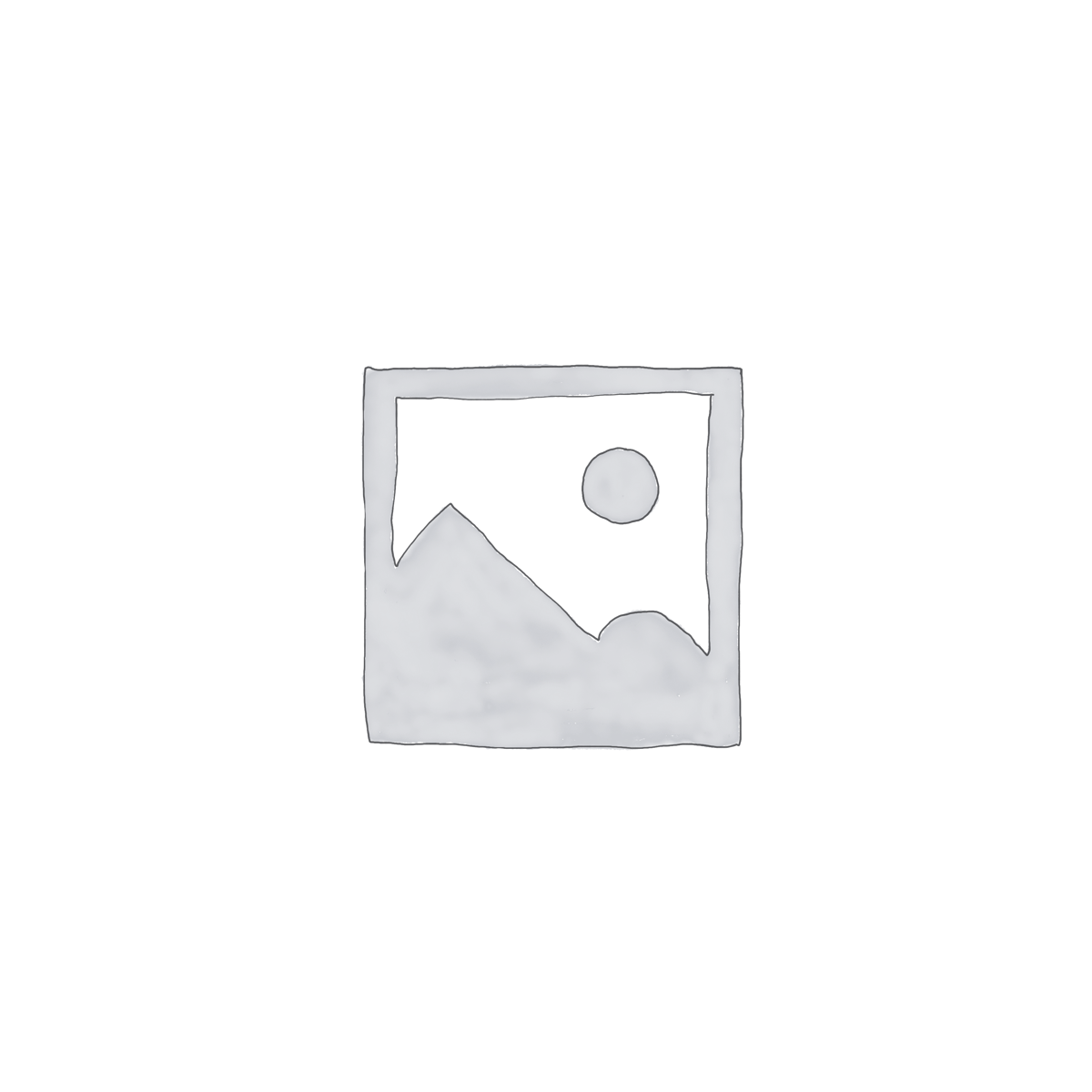
D2 Tool Steel,DIN 1.2379, X153CrMo12, SKD11,Price,Dealers,Delhi,Gurugram
- Description
Description
D2 Tool Steel (DIN 1.2379, X153CrMo12, SKD11) – Price, Dealers, Comprehensive Overview, Composition and Properties.
D2 Tool Steel, also known by its designations DIN 1.2379, X153CrMo12, and SKD11, is a high-carbon, high-chromium cold work tool steel recognized for its exceptional wear resistance, hardness, and toughness.
This type of steel belongs to the category of air-hardened tool steels, often referred to as “wind-hardened tool steel.”
Due to its superior properties, D2 tool steel is widely used in the manufacturing of dies, cutting tools, and various cold-forming applications that require excellent durability and resistance to deformation.
Composition and Properties
The chemical composition of D2 tool steel plays a significant role in determining its performance characteristics.
The mass fraction of carbon in D2 steel is relatively high, ranging from 1.4% to 1.6%, which contributes to its exceptional hardness.
Additionally, the chromium content is approximately 11% to 13%, providing excellent corrosion resistance and wear resistance.
However, due to this high carbon and chromium content, the steel exhibits a relatively lower ductility and toughness compared to other tool steels.
When subjected to heat treatment, D2 tool steel achieves an impressive hardness range of 60 HRC to 63 HRC.
This makes it ideal for applications requiring superior wear resistance.
However, this also results in a reduction in its rust-resistant properties and overall toughness.
Additionally, the surface of D2 steel is known to be difficult to polish, which can pose challenges when a high-quality surface finish is required.
As the demand for cold stamping products with higher precision, efficiency, and durability increases, tool steel needs to meet these stringent requirements.
D2 tool steel has proven to be a reliable choice for manufacturing molds and dies, providing enhanced wear resistance and extended service life.
Comparison with Cr12MoV Steel
When compared to Cr12MoV steel, D2 tool steel contains increased levels of molybdenum (Mo) and vanadium (V).
These modifications improve the microstructure of the steel and enhance its overall performance. Specifically, the changes in composition result in:
- Improved morphology of austenite grains.
- Enhanced toughness and durability.
- Superior abrasion resistance, making it more wear-resistant than Cr12MoV steel.
- Extended service life of molds and dies.
While D2 steel provides better wear resistance and longevity, it does have certain drawbacks.
Its higher yield strength and resistance to plastic deformation make forging and thermoplastic forming more challenging when compared to Cr12MoV steel.
This means that working with D2 tool steel requires specialized techniques and processes to ensure optimal results.
Chemical Composition of D2 Tool Steel
The chemical composition of D2 tool steel includes the following elements:
Element | Content (%) |
---|---|
Carbon (C) | 1.4 – 1.6 |
Chromium (Cr) | 11 – 13 |
Molybdenum (Mo) | 0.7 – 1.2 |
Vanadium (V) | 0.5 – 1.1 |
Manganese (Mn) | 0.1 – 0.6 |
Silicon (Si) | 0.1 – 0.6 |
Phosphorus (P) | Max 0.03 |
Sulfur (S) | Max 0.03 |
Each of these elements contributes to the overall properties of the steel:
- Carbon (C): Increases hardness and wear resistance.
- Chromium (Cr): Provides corrosion resistance, hardness, and toughness.
- Molybdenum (Mo) and Vanadium (V): Enhance toughness and wear resistance.
- Manganese (Mn) and Silicon (Si): Improve strength and hardenability.
- Phosphorus (P) and Sulfur (S): Kept to a minimum to prevent brittleness.
Applications of D2 Tool Steel
Due to its excellent mechanical properties, D2 tool steel is widely used in various industries, particularly for the manufacturing of complex tools that require high precision, wear resistance, and durability. Below are some of the key applications of D2 tool steel:
1. Cold Stamping Dies and Cutting Tools
D2 tool steel is well-suited for making cold stamping dies and cutting tools that require long service life and high resistance to wear. These include:
- Cold cutting tools (e.g., shear blades, punching tools).
- Thread rolling plates.
- Dies for blanking and forming stainless steel sheets.
- Cold extrusion dies and forming tools.
2. Cold Work Molds for Industrial Applications
Cold work molds made from D2 tool steel exhibit excellent performance in applications such as:
- Refrigerator compressor rear cover molds.
- Deep drawing molds.
- Stainless steel blanking dies.
D2 tool steel is often chosen for these applications because of its ability to maintain hardness and resistance to deformation under extreme working conditions.
3. Rolling Wheels and Punch Plates
Compared to Cr12MoV steel, rolling wheels and off-platform adjustment plate cold punches made from D2 tool steel have an extended service life, typically 5-6 times longer.
This makes D2 steel a cost-effective and reliable choice for applications involving repeated high-stress operations.
4. Wear-Resistant Components in Industrial Equipment
D2 steel is used in components that require high abrasion resistance, including:
- Bearings and bushings.
- Machine components subject to high friction.
- Industrial wear plates.
5. Tooling for High-Hardness Materials
Due to its superior wear resistance, D2 steel is suitable for tooling applications where materials with high hardness need to be processed. This includes:
- Blades for cutting hardened materials.
- Metal stamping tools for high-strength steel sheets.
Enhancing D2 Steel Performance with Rare Earth Elements
In some industrial applications, the addition of rare earth elements to D2 tool steel has been found to significantly improve its wear resistance and impact toughness. This results in:
- Extended service life of molds and flat steel rolled products.
- Increased durability and toughness, leading to less frequent replacements and maintenance.
- Enhanced performance in extreme conditions.
By incorporating rare earth elements, manufacturers can further enhance the quality and longevity of D2 tool steel components, making them even more competitive in high-performance applications.
Quenching and Hardening Properties
D2 tool steel undergoes a quenching process to achieve its final hardness. After heat treatment, it can reach 60-63 HRC, making it highly wear-resistant.
The steel is typically hardened through oil quenching or air hardening, with air hardening being the more common method due to its ability to reduce distortion during heat treatment.
Conclusion
D2 Tool Steel (DIN 1.2379, X153CrMo12, SKD11) is a premium-grade tool steel known for its exceptional wear resistance, high hardness, and extended durability.
It is widely used in cold work applications, including stamping dies, cutting tools, and industrial wear-resistant components.
Compared to Cr12MoV steel, D2 tool steel offers improved toughness and longevity due to its higher molybdenum and vanadium content.
Although it presents challenges in forging and thermoplastic forming, its superior performance in cold working applications makes it a preferred choice for precision tooling and high-hardness applications.
Through additional processing techniques, such as incorporating rare earth elements, the steel’s wear resistance and toughness can be further enhanced, ensuring longer service life and reduced maintenance costs.
Overall, D2 tool steel remains a versatile and reliable material for industries requiring high-performance tooling solutions.