Description
Main characteristics and applications
WW.NR. 1.2085 is used for core parts and mould bases of corrosion resistance plastic moulds or where equipment needs to be made with excellent workability and excellent corrosion resistance.
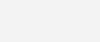
Comparable standards
DIN | W.Nr | AFNOR | AISI/SAE | JIS
|
- | 1.2085 | ~Z33CS16 | ~442+S | - |
Chemical composition (typical; in weight %)
C | Si | Mn | P (max) | S (max) | Cr | Mo | Ni
|
0.28-0.38 | <1.00 | <1.40 | 0.030 | 0.05-0.10 | 15.00-17.00 | - | - |
Production technology
EAF – LF – VD – Forging – Heat treatment QT
US specification
In according to standard EN10228-3 Class 4 and standard SEP 1921 Class E/e
Delivery condition
WW.NR. 1.2085 is delivered in quenched and tempered condition, with hardness range 280 – 325 HB (29 – 35 HRC).
Physical properties (reference values)
| 20°C | 100°C | 250°C | 500°C
|
Thermal expansion coefficient (10-6/K) | 10.5 | 10.7 | 12 | 13.2
|
Thermal conductivity (W/mk) | 22.2 | 22.7 | 21 | 24.5
|
Young modulus (Kn/mm2) | 215 | 211 | 203 | 180
|
Critical points
Ac1 | 790 °C |
Ac3 | 890 °C |
Ms | 190 °C |
Heat treatment
TREATMENT | TEMPERATURE | HOLDING TIME (HT) | COOLING | COMMENTS
|
Annealing | Heat to 850 - 880 °C | Min. H.T. for 2 minute /mm | Air or furnace | In order to obtain hardness lower than 250 HB ( 24 HRC) to improve machinability
|
Stress relieving | Heat to 590 - 650 °C | Min. H.T. for 2 minute /mm | Air or furnace | To be carried out after machining, is recommended to eliminate the residual stresses induced by mechanical working
|
Hardening | Heat to 1000-1050°C | Min. H.T. for 1 minute /mm | Air or Polymer (depending of size) | -
|
Tempering | Heat to 550 – 610°C | Min. H.T. for 3 minute /mm | Air of furnace | To be carried out after hardening. 2nd Tempering must be performed to max 30°C below tempering temperature
|