DIN 1.2316 | DIN 1.2083 ESR | Supplier | Steel
What is DIN 1.2316?
DIN 1.2316 ESR is a high-quality, corrosion-resistant tool steel widely recognized for its exceptional performance in the manufacturing of plastic molds and dies. The Electro-Slag Remelting (ESR) process enhances its purity and uniformity, resulting in superior mechanical properties and reliability. This article provides an in-depth exploration of DIN 1.2316 ESR steel, covering its chemical composition, physical and mechanical properties, heat treatment processes, applications, advantages, and comparisons with similar steel grades.
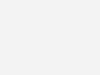
DIN 1.2316 high Hard
Chemical Composition of DIN 1.2316 ESR Steel
The chemical composition of DIN 1.2316 ESR steel is meticulously balanced to achieve its remarkable properties:
- Carbon (C): 0.33% – 0.45%
- Silicon (Si): ≤ 1.00%
- Manganese (Mn): ≤ 1.00%
- Chromium (Cr): 15.00% – 17.00%
- Molybdenum (Mo): 1.00% – 1.50%
- Phosphorus (P): ≤ 0.030%
- Sulfur (S): ≤ 0.030%
The high chromium content significantly enhances the steel’s corrosion resistance, while molybdenum contributes to its strength and toughness.
Physical and Mechanical Properties
DIN 1.2316 ESR steel exhibits a combination of physical and mechanical properties that make it suitable for demanding applications:
- Hardness: In the hardened and tempered condition, it typically achieves a hardness of 48 – 52 HRC.
- Tensile Strength: Approximately 930 MPa.
- Yield Strength: Around 800 MPa.
- Impact Strength: Approximately 20 Joules.
These properties ensure that the steel can withstand significant mechanical stresses and wear, maintaining its integrity over prolonged use.
Heat Treatment Processes
The performance characteristics of DIN 1.2316 ESR steel can be further optimized through appropriate heat treatment processes:
- Annealing: Heating the steel to 710-740°C followed by slow cooling to soften the material, enhancing its machinability.
- Hardening: Heating to 820-860°C and then quenching in oil or air to achieve the desired hardness.
- Tempering: Reheating the hardened steel to 500-700°C to adjust the hardness and toughness balance according to specific application requirements.
These processes refine the steel’s microstructure, improving its mechanical properties and suitability for various applications.
Applications of DIN 1.2316 ESR Steel
The unique combination of properties makes DIN 1.2316 ESR steel ideal for a range of applications, particularly in environments requiring high corrosion resistance and durability:
- Plastic Injection Molds: Suitable for molding chemically aggressive plastics like PVC, ensuring longevity and maintaining high-gloss finishes.
- Medical and Food-Grade Applications: Utilized in manufacturing molds for medical devices and food containers where hygiene and corrosion resistance are critical.
- Die-Casting Molds: Employed in producing molds for die-casting processes involving corrosive materials.
- Extrusion Tools: Used in tools for extruding plastics and other materials requiring high surface quality.
These applications benefit from the steel’s ability to maintain structural integrity and surface finish in challenging environments.
Advantages of DIN 1.2316 ESR Steel
DIN 1.2316 ESR steel offers several advantages that make it a preferred choice in various industries:
- Enhanced Corrosion Resistance: The high chromium content provides superior resistance to corrosive environments, reducing maintenance and extending the lifespan of components.
- Excellent Polishability: Achieves a high-quality surface finish, essential for producing aesthetically pleasing plastic products.
- High Wear Resistance: Maintains dimensional stability and performance under repetitive use, ensuring consistent product quality.
- Good Toughness: Withstands mechanical stresses and impacts, reducing the risk of cracking or failure during operation.
These benefits contribute to improved performance, reduced downtime, and cost savings in manufacturing processes.
Comparison with Similar Steel Grades
When selecting a tool steel, it’s important to consider how DIN 1.2316 ESR compares to other grades:
- DIN 1.2083: While both steels offer good corrosion resistance, 1.2316 ESR has a higher chromium content, providing enhanced resistance and toughness, making it more suitable for aggressive environments.
- AISI 420: Similar in composition, but DIN 1.2316 ESR undergoes the ESR process, resulting in improved purity, uniformity, and mechanical properties.
These distinctions help in selecting the appropriate steel grade based on specific application requirements.
Conclusion
DIN 1.2316 ESR steel stands out as a high-performance tool steel, offering exceptional corrosion resistance, polishability, wear resistance, and toughness. Its balanced chemical composition and enhanced properties due to the ESR process make it an ideal choice for demanding applications in the plastic molding, medical, and food industries. By understanding its characteristics and advantages, manufacturers can make informed decisions, ensuring optimal performance and longevity of their tools and components.