
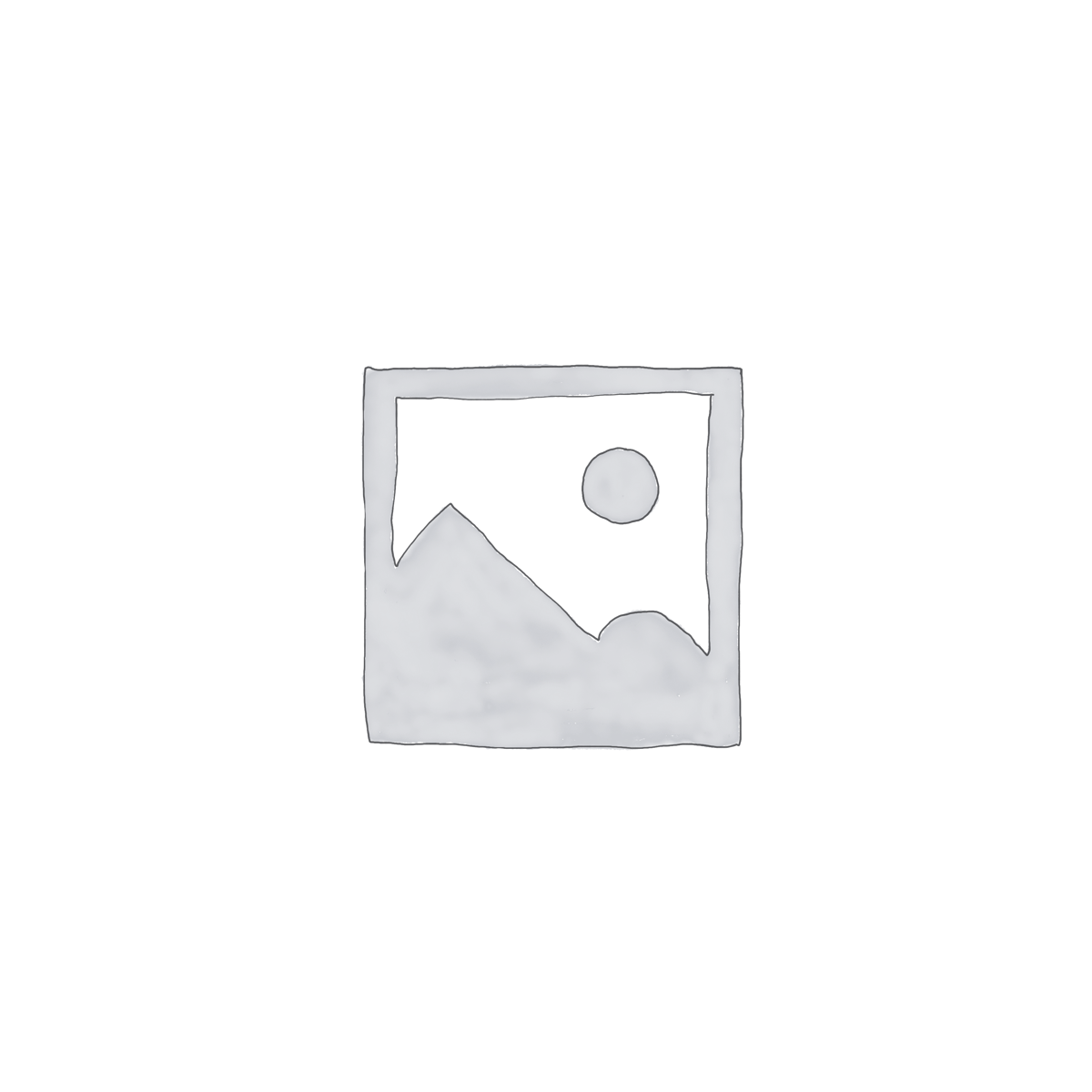
P20 High Hard Steel
- Description
Description
P20 High Hard Steel Grade: An In-Depth Overview.
P20 High Hard Steel is a versatile, pre-hardened steel commonly used in the manufacturing of plastic injection molds, die-casting tools, and various other applications requiring exceptional toughness and machinability.
Known for its balanced combination of hardness, toughness, and machinability, it has become a preferred choice among toolmakers and manufacturers worldwide.
This article delves into the composition, properties, applications, and advantages of P20 High Hard Steel, providing a comprehensive understanding of this widely used material.
1. Chemical Composition of P20 High Hard Steel
The chemical composition of P20 High Hard Steel is a critical factor contributing to its excellent mechanical and physical properties. The typical composition includes:
Carbon (C): ~0.28% to 0.40% – Provides hardness and wear resistance.
Silicon (Si): ~0.20% to 0.40% – Improves strength and resistance to oxidation.
Manganese (Mn): ~0.60% to 1.00% – Enhances toughness and wear resistance.
Chromium (Cr): ~1.00% to 2.00% – Increases hardness, corrosion resistance, and wear resistance.
Molybdenum (Mo): ~0.30% to 0.55% – Improves toughness and strength, especially at elevated temperatures.
Nickel (Ni): ~0.90% to 1.20% – Enhances toughness and improves structural stability.
The combination of these elements results in a material with high strength, excellent toughness, and good machinability.
2. P20 High Hard Steel Mechanical and Physical Properties.
P20 High Hard Steel is characterized by the following properties:
Hardness:-
P20 steel Typically supplied in the pre-hardened condition with a hardness of 28 to 34 HRC.
P20 High Hard Typically supplied in the pre-hardened condition with a hardness of 34 HRC to 38 HRC.
It is suitable for many applications without requiring additional heat treatment.
Toughness:-
Excellent toughness ensures resistance to cracking and deformation under mechanical stress.
Machinability:-
The material offers superior machinability, making it easier to fabricate molds and dies with intricate designs.
Polishability:-
P20 High Hard Steel can achieve a high surface finish, which is essential for plastic mold applications where surface quality directly affects the final product.
Corrosion Resistance:-
While not as corrosion-resistant as stainless steel, it provides moderate resistance due to the chromium and nickel content.
Weldability:
Suitable for welding operations, which are often required for mold repairs or modifications.
3. Advantages of P20 High Hard Steel
The popularity of P20 High Hard Steel stems from its numerous advantages, including:
- Pre-Hardened Condition: Delivered pre-hardened, eliminating the need for time-consuming and costly heat treatment processes.
- Consistent Performance: Its uniform hardness and toughness provide consistent performance across a wide range of applications.
- Cost-Effective: Offers a balance between performance and cost, making it an economical choice for tool and mold manufacturing.
- Durability: With its excellent wear resistance and toughness, it ensures long-lasting performance, reducing maintenance and replacement costs.
- Versatility: Suitable for a variety of applications, from injection molding to die-casting, ensuring adaptability in diverse industries.
Applications of P20 High Hard Steel.
P20 High Hard Steel is used in various industries, primarily in tooling and mold-making, due to its exceptional properties. Key applications include:
Plastic Injection Molds:-
Its polishability and toughness make it ideal for manufacturing plastic injection molds, particularly for high-volume production. It is commonly used for molds requiring medium to large dimensions.
Die-Casting Dies:-
Its ability to withstand high pressure and elevated temperatures makes it suitable for die-casting dies, especially in aluminum, zinc, and magnesium alloys.
Blow Molds:-
The high surface finish capability of P20 High Hard Steel is advantageous for blow molds used in the production of plastic containers and bottles.
Extrusion Dies:-
Its wear resistance and machinability are critical for extrusion dies used in shaping thermoplastics and thermosets.
Automotive and Aerospace Components:
Used in prototypes, tooling, and fixtures, P20 High Hard Steel ensures precision and durability in demanding applications.
General Tooling:-
Its versatility extends to a variety of tools, such as gauges, jigs, and fixtures, where strength and machinability are essential.
Heat Treatment and Surface Modifications
Although P20 High Hard Steel is typically used in its pre-hardened state, it can undergo additional treatments to enhance specific properties:
Heat Treatment:-
Hardening: Can be hardened to higher levels (40–50 HRC) for applications requiring superior wear resistance.
Annealing: Performed to soften the material, making it easier to machine for complex designs.
2. Surface Treatments:-
Nitriding: Enhances surface hardness and wear resistance without affecting core toughness.
Chrome Plating: Improves corrosion resistance and wear resistance for demanding environments.
PVD/CVD Coatings: Applied for increased tool life in high-abrasion applications.
6. Limitations of P20 High Hard Steel
Despite its excellent properties, P20 High Hard Steel has a few limitations:
Moderate Corrosion Resistance:
Not suitable for highly corrosive environments; stainless steel is preferred in such cases.
Limited Hardness Range:
The hardness in the pre-hardened state may not be sufficient for all applications, necessitating additional treatments.
Surface Defects:
Improper machining or polishing can result in surface defects, affecting the quality of the final product.
7. Alternative Materials
In some cases, alternative materials may be considered depending on the specific requirements of the application:
– H13 Tool Steel: Preferred for applications requiring high thermal resistance and toughness.
– 718 Steel: Offers enhanced polishability and corrosion resistance.
– 420 Stainless Steel:
Ideal for applications demanding superior corrosion resistance and mirror-like finishes.
8. Conclusion
P20 High Hard Steel stands out as a reliable, versatile, and cost-effective material for tooling and mold-making applications.
Its balanced combination of hardness, toughness, and machinability makes it a go-to choice for industries like plastics, die-casting, and automotive manufacturing.
While it has some limitations, the ability to enhance its properties through surface treatments and alternative processing methods ensures its continued relevance in modern manufacturing.
Choosing P20 High Hard Steel means opting for a material that delivers consistent performance, durability, and adaptability—making it a cornerstone of tool and die engineering.